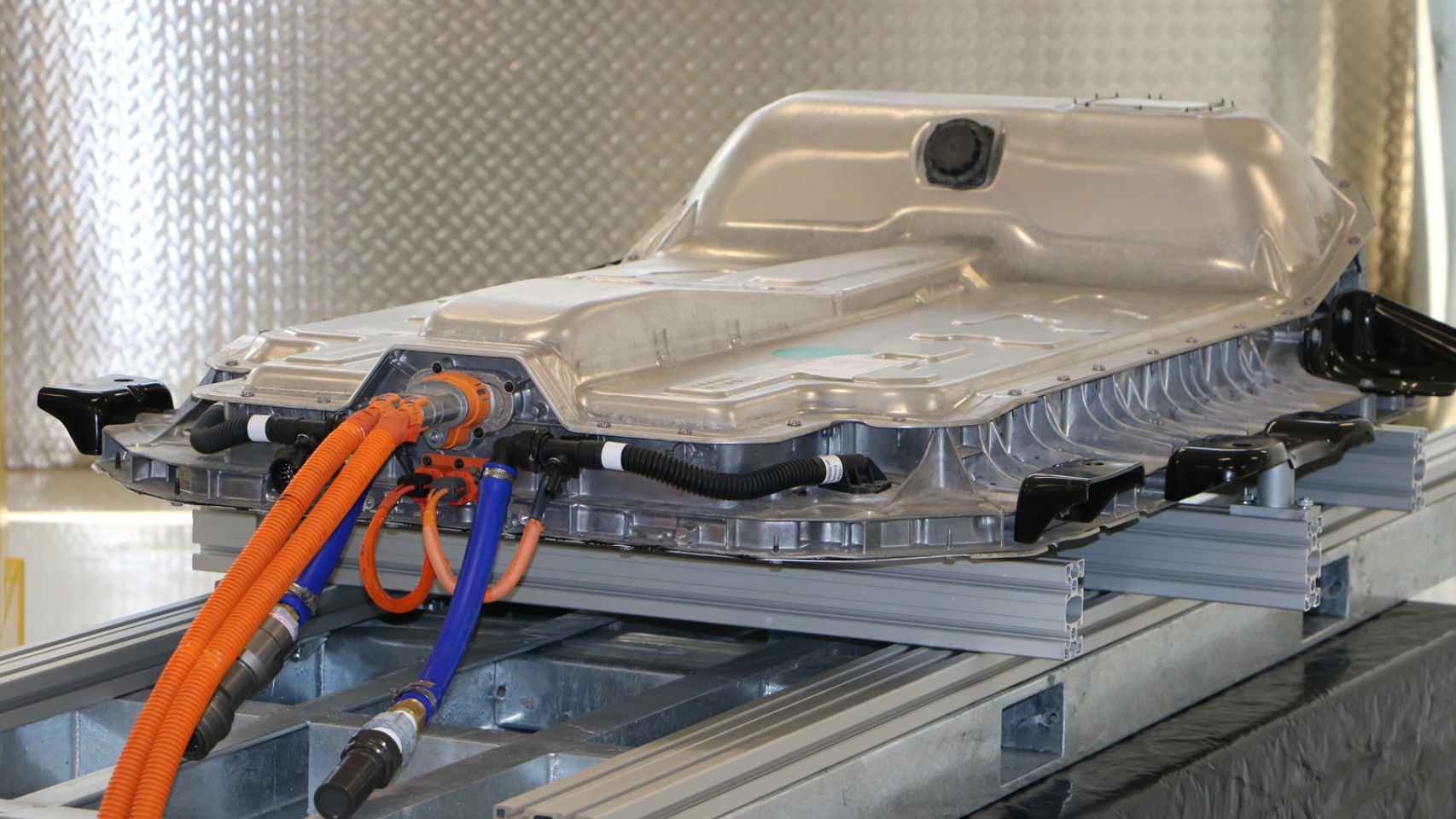
Una batería de coche eléctrico en pleno proceso de pruebas.
De 40º bajo cero a 60º: así prueban al ‘límite’ las baterías de los coches eléctricos
- Visitamos el último centro de tecnología inaugurado por Stellantis en Italia que garantiza la fiabilidad de estos componentes.
- Coches nuevos: precios y ofertas | Coches híbridos | Coches eléctricos
En un coche eléctrico, las baterías son fundamentales. Sin embargo, construir este elemento es un proceso complejo y costoso. Además, tiene diversas etapas. La primera es el desarrollo de las celdas, que son elementos que tienen la forma de un ladrillo fino metálico.
Estas celdas son las que se construyen en las gigafactorías (España contará con al menos una en Sagunto). Y después de su fabricación, se unen y se conectan, para más tarde introducirse en una estructura protectora.
Esto es lo que conforma la batería y se hace en los talleres de baterías. Y en España, ya hemos podido ver, al menos, los talleres de baterías de Stellantis en Vigo y Zaragoza.
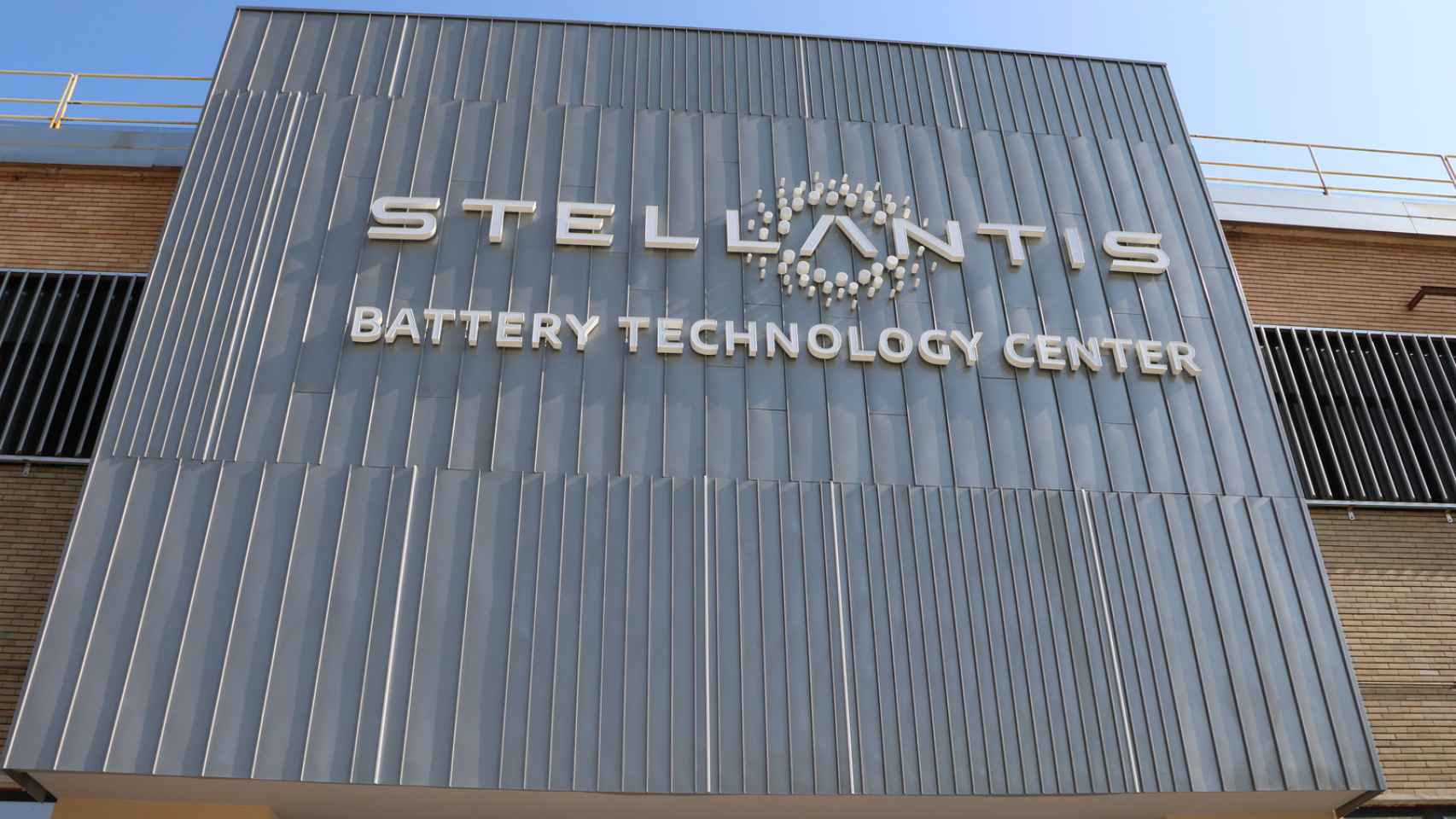
Así es el centro de tecnología de Stellantis en Turín (Italia).
Tras el ensamblaje de la batería, llega el momento de su introducción y conexión al vehículo. Sin embargo, previamente, también los fabricantes necesitan hacer otro paso. Y este no es otro que el hecho de realizar pruebas a estas baterías ensambladas, así como a los módulos, para saber que todo está correcto.
Como es lógico, no pueden hacer pruebas a todas las baterías ensambladas (Stellantis, en 2022, comercializó cerca de 300.000 coches eléctricos), pero sí a un buen número de ellas para controlar todos los procesos.
Centro Tecnológico de Baterías de Stellantis en Milán
El lugar elegido para este control de las baterías es el Centro Tecnológico de Baterías, el primero de este constructor que ha sido desarrollado en Turín (Italia), y al que EL ESPAÑOL ha tenido acceso. En concreto, el lugar es la fábrica de Mirafiori, centro en el que antes se fabricaban modelos como el Alfa Romeo Mito y actualmente se ensambla el Fiat 500 eléctrico.
Este centro, que ha supuesto una inversión de 40 millones de euros para Stellantis (y será el primero de varios), es el encargado de diseñar, desarrollar y probar los paquetes de baterías, los módulos, las celdas de alta tensión y el software. Cuenta con 100 empleados que se encargan de realizar y supervisar ensayos de estrés climático y su vida útil. Además, también en este centro, calibran el software del sistema de gestión de baterías (BMS).
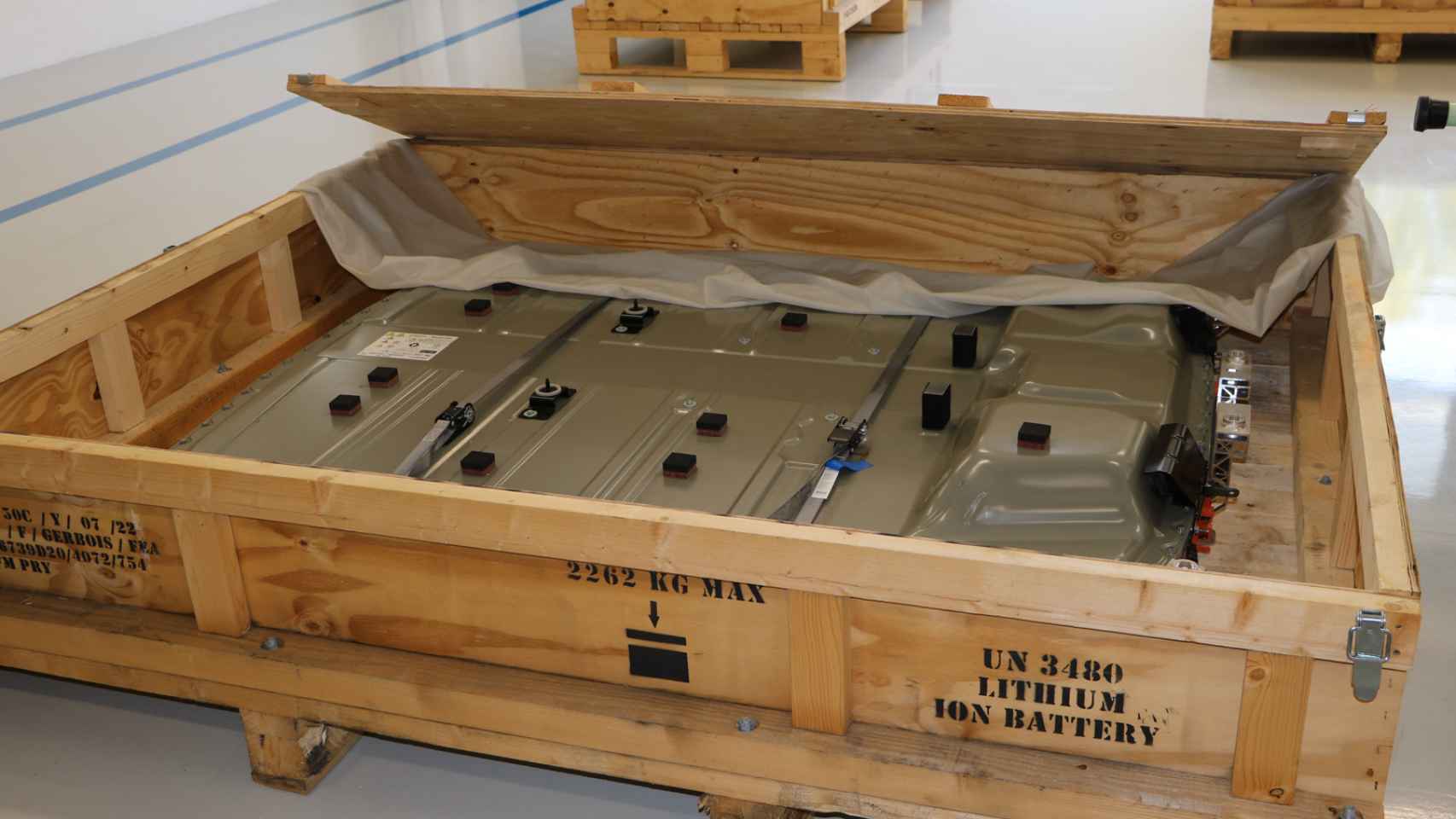
Las baterías llegan en estas cajas protectoras de madera.
Una factoría con la última tecnología
Nada más llegar al Centro Tecnológico de Baterías la primera impresión es que Stellantis ha sabido transformar una mítica factoría en un centro con la última tecnología. Aquí, por ejemplo, ya no vemos líneas de producción ni cadenas de montaje ni tan siquiera coches. Ahora, el espacio es más luminoso, más aséptico…
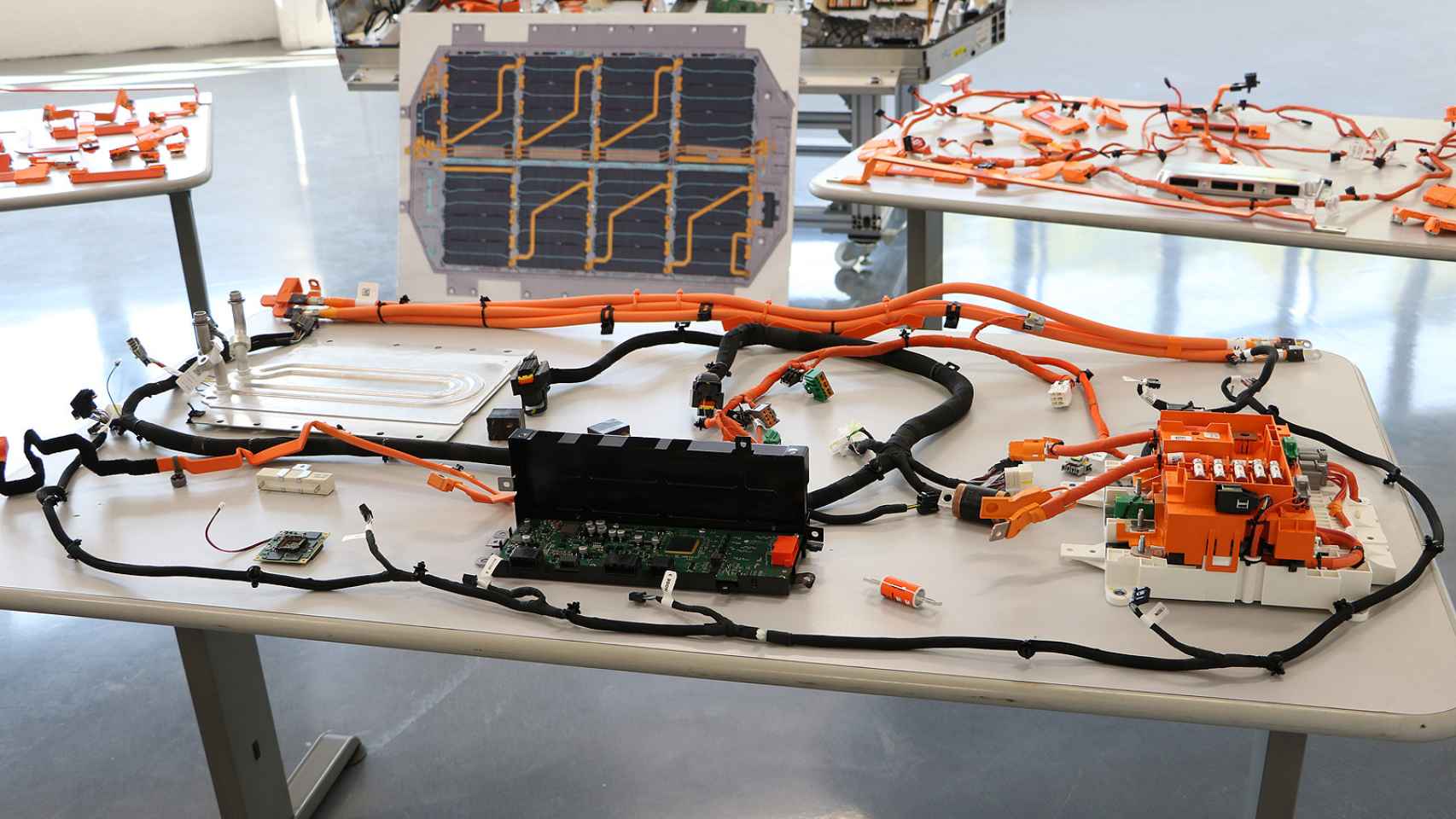
Estos son los componentes que tiene una batería.
Lo primero que nos enseñan es cómo llegan las baterías, que lo hacen guardadas en enormes cajas de madera. Al final hay que tener en cuenta que estas baterías superan los 300 kilos de peso y son difíciles de manejar.
Una vez que llegan las cajas, las abren y empieza la preparación de las baterías y las diferentes pruebas. Unas pruebas que pueden durar minutos o incluso semanas, señalan desde la planta.
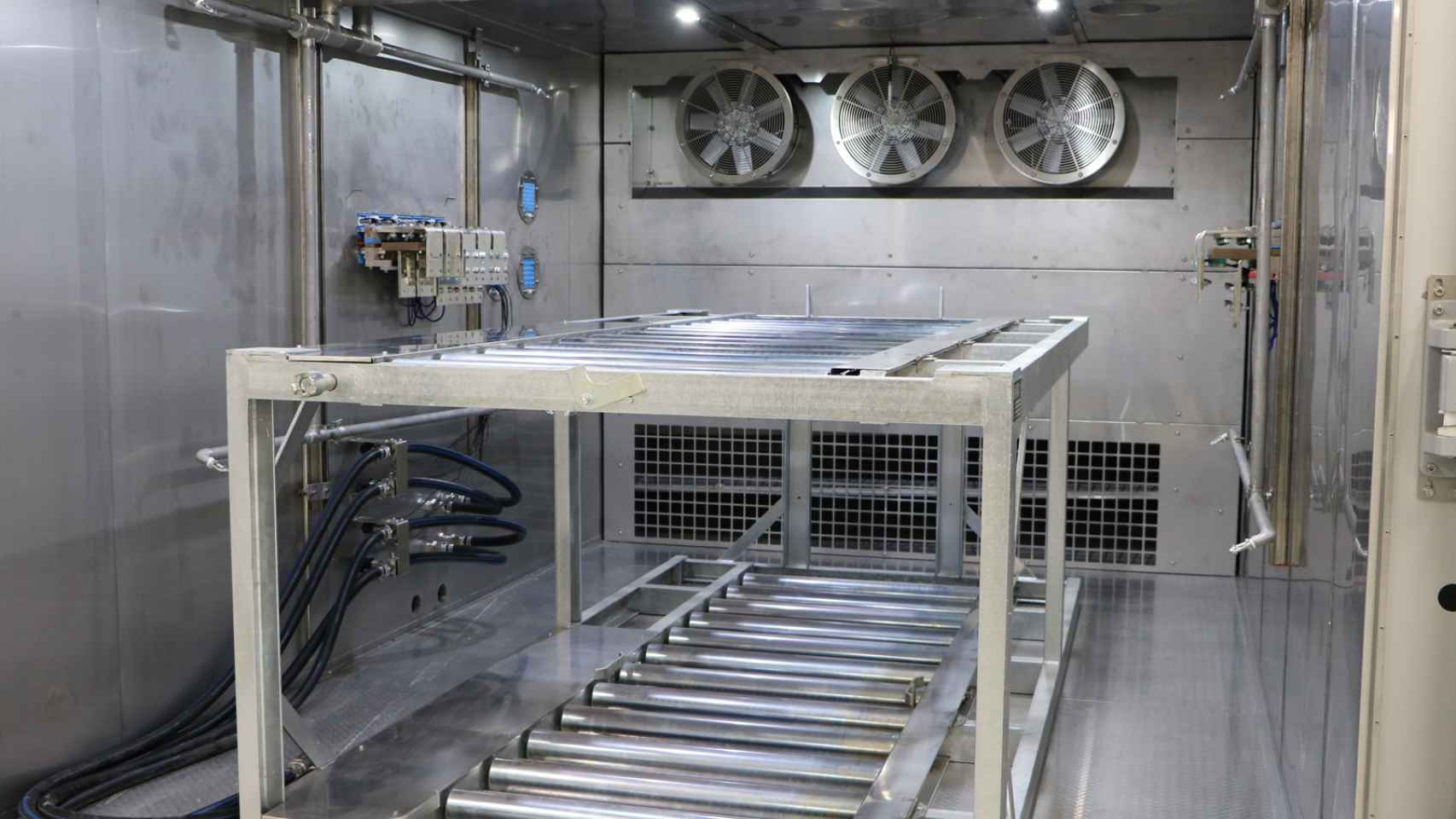
Una de las cámaras frigoríficas de este centro.
Enormes cámaras frigoríficas
En total, son 8.000 metros cuadrados distribuidos en tres niveles. Accedemos a la planta de calle y vemos algunas de las cámaras climáticas de ensayos. Son 32 enormes frigoríficos en forma de contenedores, 24 de ellos para probar las baterías y ocho para probar celdas. Se pueden probar hasta 47 baterías en paralelo. Además, las ocho cámaras para celdas pueden probar 96 celdas en paralelo.
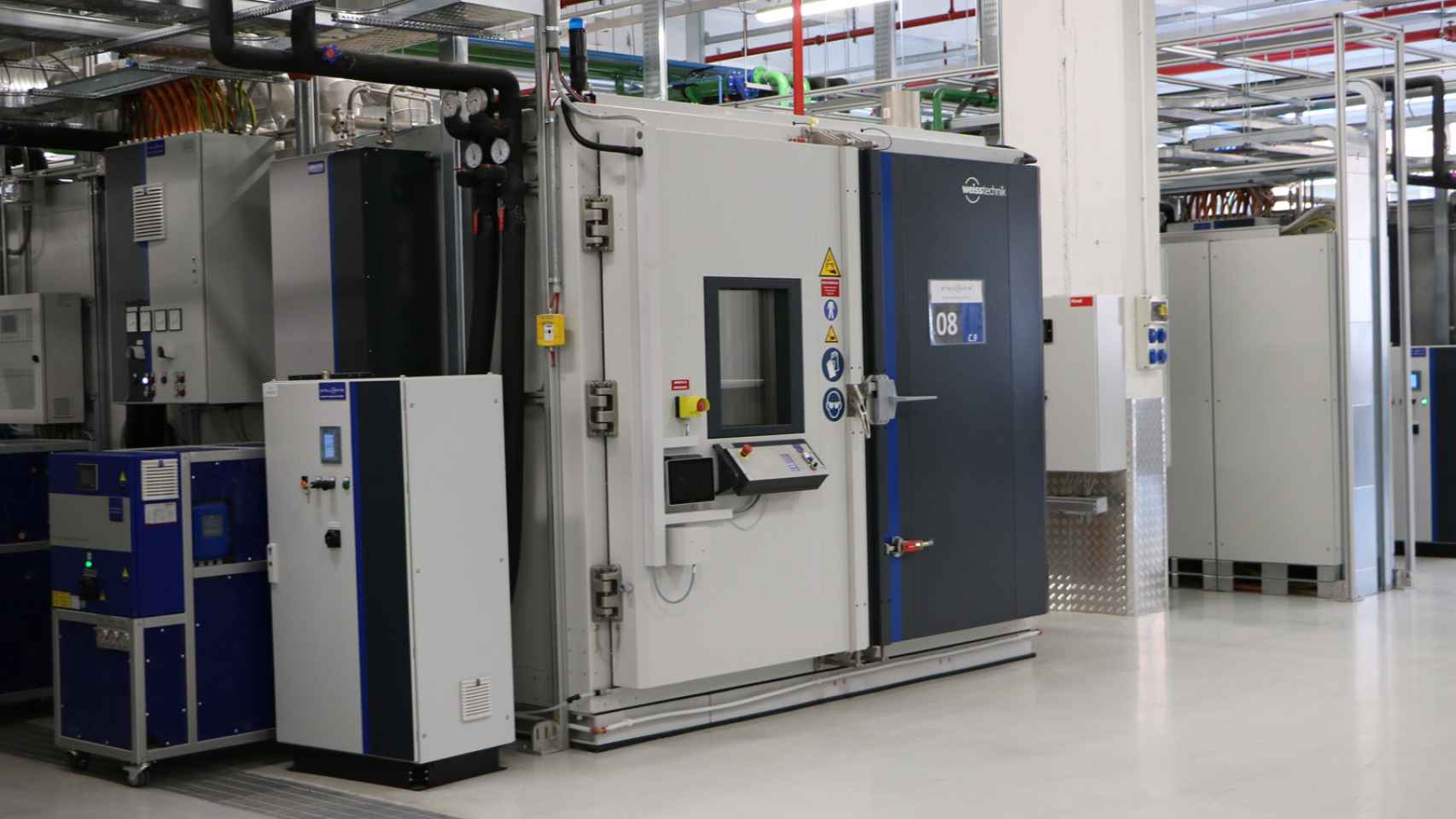
Alguno de los módulos del centro de tecnología de Turín.
Estas cámaras climáticas lo que hacen es controlar la humedad y la temperatura y son capaces de comprobar el funcionamiento de las baterías entre los 40 grados bajo cero y los 60 grados. Además, son pueden cambiar 20 grados en sólo un minuto.
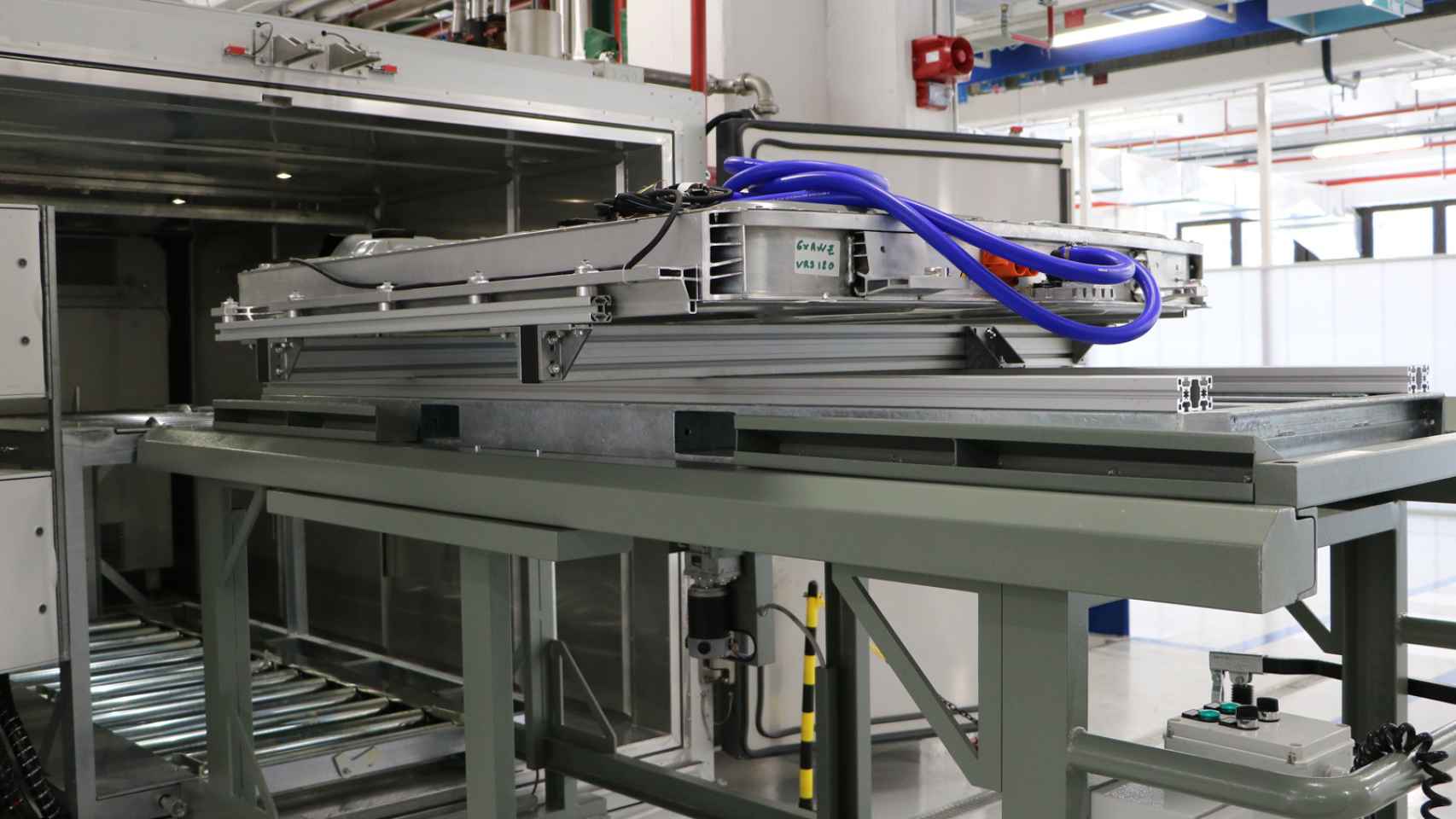
Una batería se introduce en la cámara frigorífica.
400 GWh de capacidad de baterías en 2030
Este centro tecnológico de baterías es un paso más, por tanto, en la cadena de valor de las baterías, desde el diseño, el desarrollo y los ensayos hasta la producción y constituye el eje de la estrategia de Stellantis de producir vehículos eléctricos.
Para alcanzar estos objetivos, la compañía se está asegurando una capacidad total aproximada de 400 GWh con sus baterías, para lo que contará con el apoyo de seis plantas de fabricación en Norteamérica y Europa, lo que se conocen como gigafactorías. Además, el grupo no descarta la posibilidad de instalar nuevas gigafactorías adicionales a las seis ya planificadas.
También te puede interesar...
- Todos los precios y ofertas de los coches nuevos en España
- Precios y ofertas de coches híbridos | Coches híbridos enchufables | Coches eléctricos
- Listado con los principales coches con etiqueta eco
- Coches con etiqueta cero de la Dirección General de Tráfico
- Precios y ofertas de coches de segunda mano
- Todos los coches SUV | Coches SUV medianos | Coches SUV urbanos