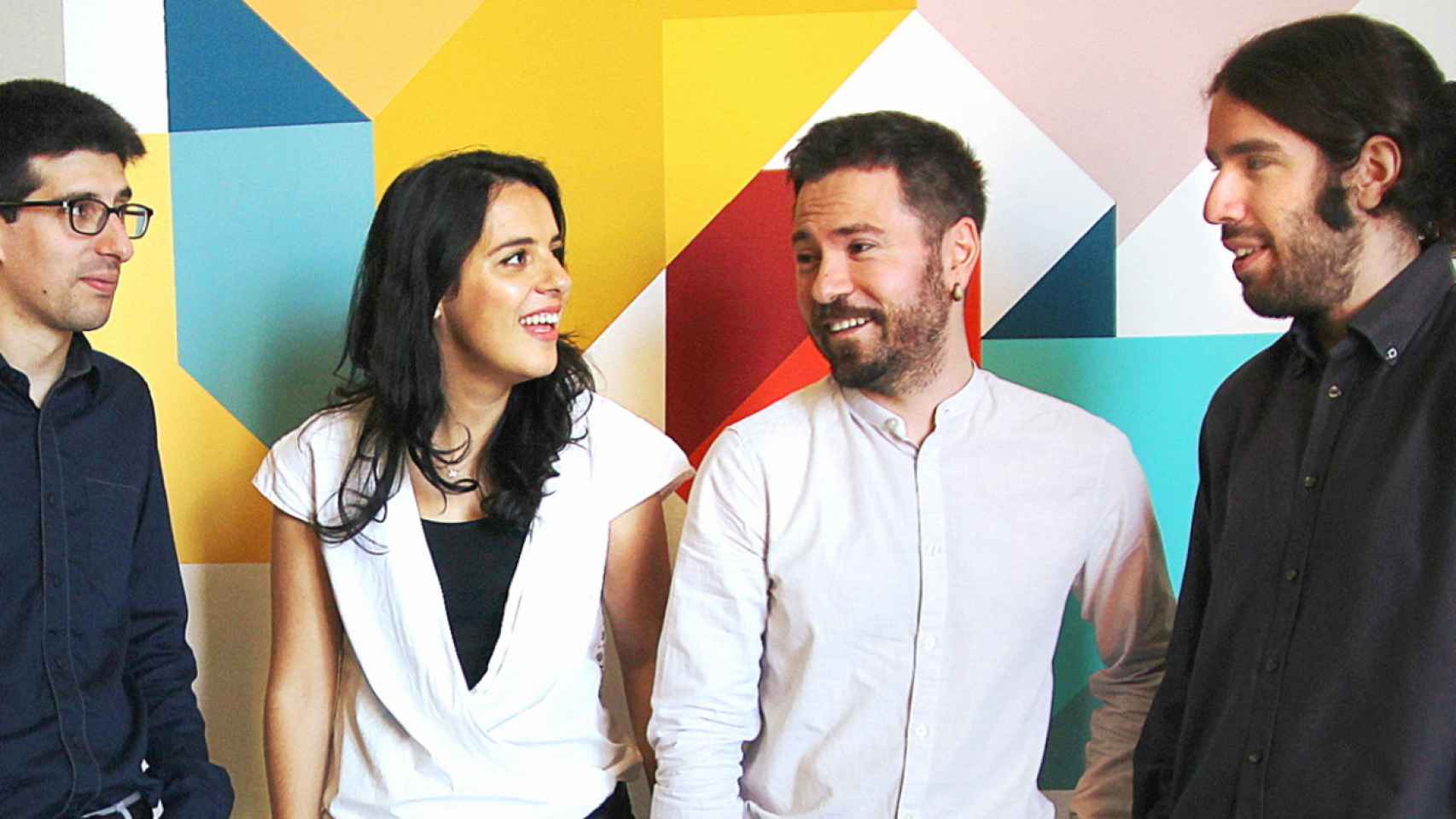
Los cuatros socios fundadores de la startup española Onyriq.
Innovadores
Este material para impresión 3D de la española Onyriq puede ser blando o duro
El primer uso que propone la startup es para prótesis cómodas y estructurales
13 agosto, 2018 07:00Cuando tres químicos combinan su talento con un ingeniero aeroespacial, el resultado es impredecible. Así les ha ocurrido a Ainhoa Tolentino, Joseba Luna, Mikel Galino y Oriol Gásquez quienes, desde Onyriq, tratan de potenciar la I+D en un ámbito muy concreto, los polímeros.
Tras un periplo por universidad, empresa privada e institutos tecnológicos, estos cuatro amigos decidieron reunirse en 2016 para lanzar su propio proyecto. “Veíamos que la I+D a veces se quedaba en el cajón y no llegaba a tener un impacto económico y social representativo”, recuerda Galino.
Su conocimiento se centra en los materiales poliméricos. Este ‘know how’ le ha permitido, como a muchas startups, captar sus primeros ingresos ofreciendo servicios de I+D a terceros. “La ventaja de los polímeros es que no son sectoriales, están en todos los ámbitos, desde los adhesivos hasta los tejidos”, comenta Galino. Onyriq es capaz tanto de optimizar procesos y materiales que ya tiene una compañía como de crear otros desde cero.
Esta línea de trabajo (y de ingresos) le ha servido de colchón a la startup para trabajar en su I+D propia. Y aquí está desarrollando un producto nuevo en el mercado: un material que puede presentar diferentes grados de dureza en una sola impresión en 3D.
Dos tecnologías de fabricación aditiva son las más populares en el mercado. La primera es la más conocida y responde a la impresión 3D más popular. Se trata del Modelado por deposición fundida (FDM) que consiste en superponer capas de material hasta conformar la pieza. La principal desventaja de esta técnica es que las propiedades finales del producto (resolución, desempeño y productividad) son limitadas.
Otra técnica es el sinterizado selectivo por láser (SLS), que utiliza un láser para fundir el material. Esta tecnología supone un salto en prestaciones y productividad. Sin embargo, aún tiene sus limitaciones, principalmente, en cuanto a la disponibilidad de materiales.
Además de las desventajas particulares de cada tecnología, existen otras "inherentes" a la impresión 3D, como son las reducidas propiedades en el eje z, debido a la adhesión entre capas, o la imposibilidad de trabajar con diferentes materiales en una sola impresión. “Las distintas capas de esos materiales tienen que adherirse y la interacción entre dos polímeros de diferente naturaleza normalmente no es buena, la pieza no resulta lo suficientemente funcional”, explica Galino.
Para dar una respuesta a la industria, Onyriq está diseñando un único material que puede presentar diferentes propiedades mecánicas. El equipo ha sintetizado un material de forma que, cuando es expuesto a un haz de energía, pueda crear unas zonas flexibles y otras rígidas a elección del técnico. “Según la intensidad del láser, se modifican los enlaces químicos a nivel molecular, traduciéndose de esta manera en un comportamiento macroscópico diferenciado”, comenta el cofundador. Esta escala de rigidez se traslada proporcionalmente a las propiedades mecánicas de la pieza final.
Prótesis para amputados
No es casualidad. Los emprendedores han ideado este material con un primer uso muy concreto: las prótesis para amputados. “Cada paciente es un mundo”, dice Galino. Los muñones tienen muchas terminaciones de vasos sanguíneos y nerviosas. “Son zonas muy sensibles, que requieren comodidad; pero a su vez necesitan un elemento que aporte una función estructural”.
Actualmente, la pieza de la prótesis donde se aloja el muñón (llamada encaje) está fabricada con resina termoestable reforzada con fibra de carbono. Para su producción, el ortopeda tiene que hacer un molde de escayola a medida, crear un positivo y realizar un rebaje manual. El paciente tiene entonces que probarse la prótesis provisional y evaluar la comodidad y la necesidad de hacer ajustes. “Es un proceso que suele requerir varias visitas”, comenta.
Además, el encaje es una pieza que debe ajustarse a la perfección a la morfología concreta del miembro amputado, por lo que cualquier cambio en el volumen o forma del muñón implica la necesidad de realizar uno nuevo. Por ello, y dependiendo de la actividad del paciente, su fabricación es un proceso que puede ser necesario repetir cada año.
Onyriq pretende acabar con estos inconvenientes. Simplemente con un escáner manual al paciente, se puede obtener un modelo 3D digital del muñón. “A partir de este modelo se diseña el encaje y sus diferentes zonas de rigidez de acuerdo a las indicaciones del ortopeda; la información se envía a la impresora 3D, que lo fabrica utilizando nuestro material, de forma que se reproducen las diferentes durezas para cada zona en función de los requisitos preestablecidos”, explica Galino. Y todo, en cuestión de un día. Además, añade, el coste se reduce enormemente (tanto para la persona como para el ortopeda).
La startup está en pleno proceso de validación de la prueba de concepto y cuenta con varios partners interesados en colaborar con ellos.