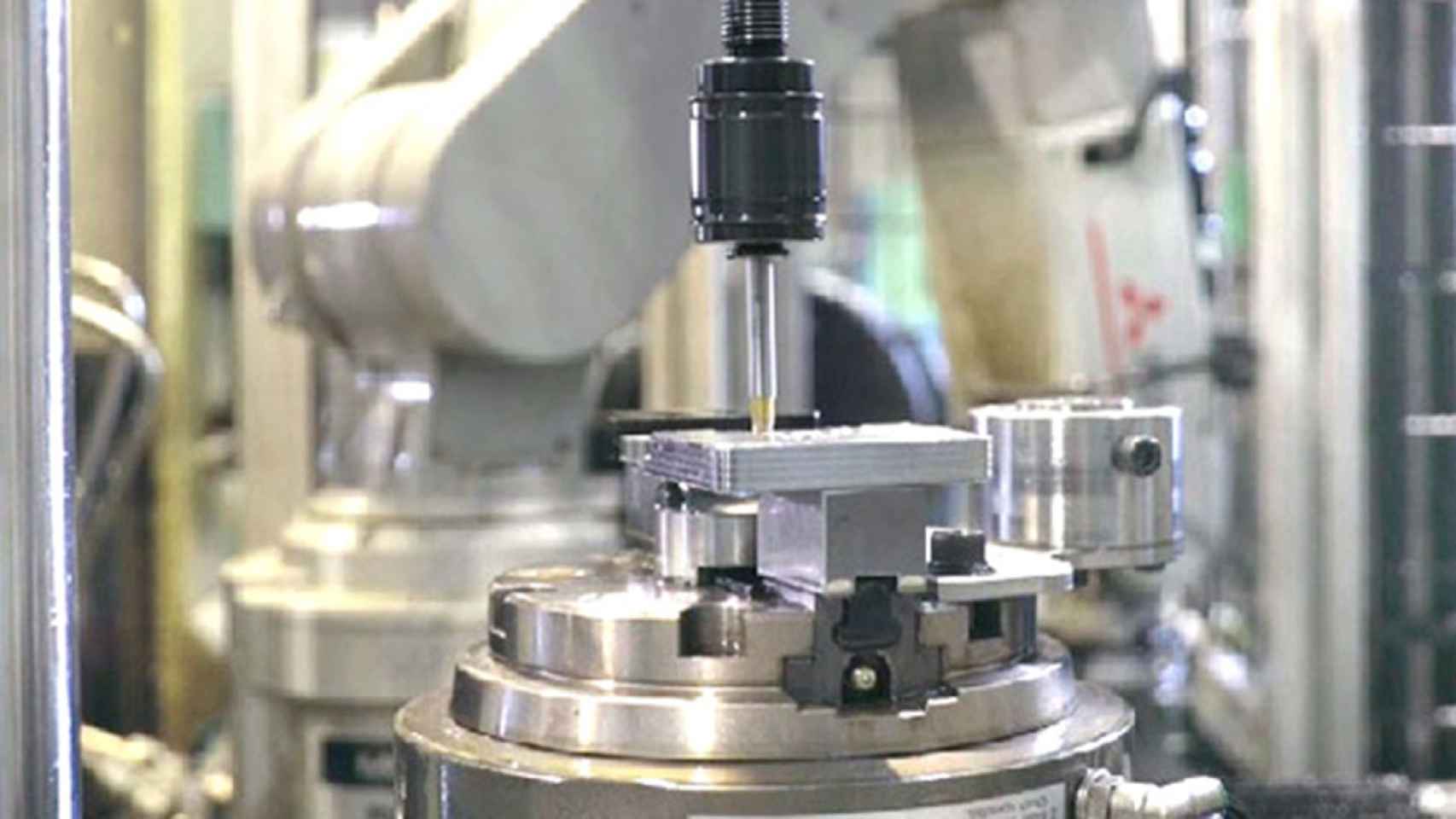
Una de las soluciones de taladrado y roscado de Erlo Group.
Innovadores
Esta máquina, conectada y automatizada, detecta los fallos en roscas en la cadena de producción
Tekniker y Erlo Group aplican big data y cloud computing para lograr más fiabilidad y mayor eficiencia en las cadenas de producción de sus clientes de automoción y aeronáutica
3 abril, 2020 11:00Interceptor es sistema que cuenta con una máquina conectada y automatizada capaz de gestionar la calidad de la rosca en tiempo real y detectar de forma precoz posibles fallos en la propia cadena de producción. Es un proyecto en el que colaboran el centro tecnólogico vasco Tekniker y la empresa Erlo Group para monitorizar, con tecnología big data, las piezas y poder conocer su estado y los fallos en tiempo real. De este modo se mejora tanto la fiabilidad como la disponibilidad de los equipos, al poder meedir el desgaste de las piezas.
Erlo Group, especializada en soluciones customizadas de alta productividad de taladrado y roscado, ha identificado que "conseguir información sobre la calidad de la rosca es de vital importancia para clientes de distintos sectores como la automoción o la aeronáutica", por lo que tener disponible esta información en tiempo real y en la nube permite "una detección precoz de aquellas roscas de menor calidad", con lo que se reducen los costes en la cadena de producción y se gana en eficiencia, aseguran en un comunicado desde le centro tecnológico.
Esta máquina conectada integra tecnologías como big data para recabar esta información. Se trata de un comprobador de roscas que "ofrece datos accesibles en la nube y que se puede monitorizar en tiempo real" para obtener datos críticos como anomalías con las que predecir fallos que se puedan generar.
Esta propuesta tecnológica se basa en la adaptación de la plataforma SAM (Smart Asset Managemenet) de Tekniker, que permitirá el almacenamiento y posterior análisis de los datos recibidos. Además de la propia plataforma, es necesaria la conexión, recogida y almacenamiento de la información registrada mediante un datalogger para ponerla a disposición de Erlo Group, lo que, además, permitirá que las máquinas puedan incluirse en el futuro en otros sistemas de control de la producción.
Además, al almacenar esta información en la nube las empreas pueden tener la trazabilidad del proceso y así disponer de información relevante de seguridad en caso de que se produzca un incidente. Asimismo, se podrá conocer el origen del problema cuando se produzca un fallo en una pieza, señalan en este comunicado.