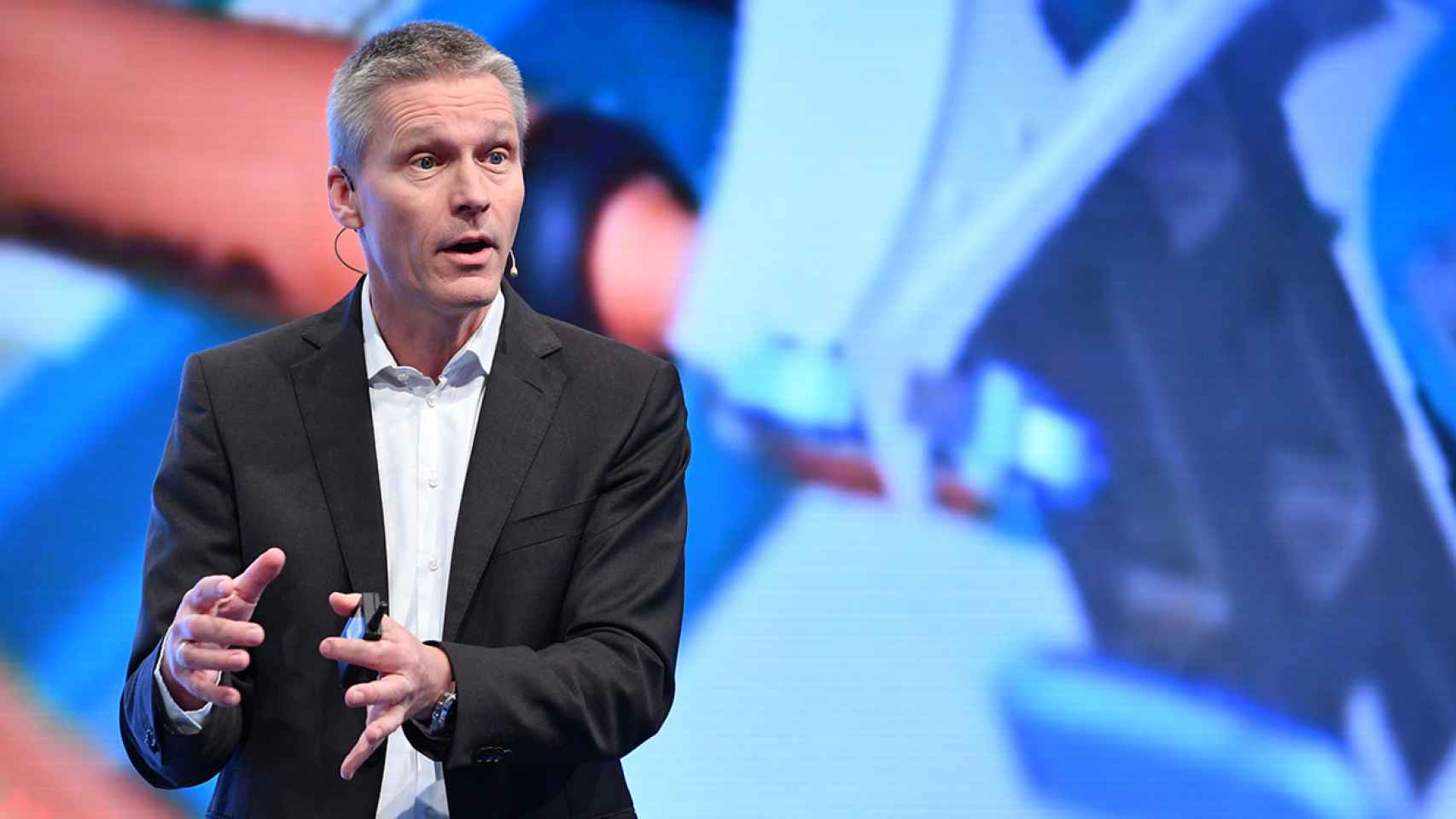
Jan Michael Mrosik, CEO de la Digital Factory Division Siemens.
Innovadores
Tres gemelos virtuales para liderar la industria digitalizada
La selección natural llega a las plataformas que compiten por digitalizar los centros productivos, el CEO de Digital Factory Division de Siemens vaticina su integraciónrnrn
13 noviembre, 2018 07:00Cuando hablamos de digitalización nos referimos sobre todo a optimización del proceso de producción. La plataforma de innovación digital de Siemens conecta toda la cadena, desde el diseño del producto hasta su uso. Nuestra solución permite tener un absoluto control de la producción y también desarrollar y optimizar todo el proceso de manera virtual, a través de los gemelos digitales (digital twins)", explica Jan Michael Mrosik, CEO de la Digital Factory Division del grupo alemán, de visita en Barcelona esta semana para participar en el Gartner Symposium/ITxpo, el encuentro europeo más importante de CIOs y ejecutivos seniors de IT, en el que se presentan las últimas líneas estratégicas de negocio, liderazgo y nuevas tecnologías.
Las soluciones de Siemens integradas en la plataforma colaborativa Teamcenter permiten el diseño de cualquier producto, "ya sea coche, barco o avión, por complicado que sea", apostilla Mrosik, y para cualquier sector industrial y tamaño de empresa. El grupo ofrece al cliente todos lo que necesita para desarrollar el diseño: la mecánica, la electrónica y el software, y "además también le facilitamos el software para simular el diseño, para fabricar un duplicado virtual del producto. Con él, puede verificar, antes de fabricar, que todo es correcto y si no lo es, efectuar los cambios que crea oportunos hasta tener una copia virtual perfecta del producto", comenta.
Esta duplicidad virtual también se aplica a la cadena de producción, en cada uno de los procesos. "Construimos una factoría real en el mundo virtual. De esta manera, ofrecemos tota la capacidad de automatización productiva".
En una tercera fase, denominada Gemelo Digital del Rendimiento (Digital Twin Performance) se conecta producto y producción. A través de la utilización de datos de sensores instalados en los productos, se determina su rendimiento en tiempo real, las condiciones en las que opera y los cambios que se producen a lo largo de su vida útil. Con toda esta información, el gemelo virtual evoluciona y se actualiza, y refleja cualquier cambio que el producto haya sufrido en su ciclo de vida.
Esta operativa, aplicada también al diseño y a la cadena de producción, produce un flujo de datos que se retroalimentan continuamente. Se crea una historia digital que permite el seguimiento de cada una de las etapas, un bucle que permite a las empresas optimizar productos, cadena de producción y rendimiento de manera continuada y a un mínimo coste.
Mrosik sintetiza la solución digital de Siemens: "Digital Twins del producto es un modelo matemático del producto en el mundo virtual. Digital Twins de la producción es un modelo matemático de la producción en el mundo virtual. Y Digital Twins del rendimiento es un modelo estadístico del producto y la producción en el mundo real". Aquí es donde se encuentran big data e inteligencia artificial.
"Y es aquí donde podemos interactuar realmente. El cliente podrá utilizar data analytics para redefinir sus modelos de producto y producción, y mejorarlos. El análisis de datos es una pieza extremadamente importante en todo el proceso de digitalización, porque permite la verificación del modelo que ha sido creado con anterioridad y te informa de cómo funcionará en el mundo real», apostilla.
Y pensando ya en internet de las cosas (IoT), la conexión entre productos inteligentes es también fundamental. Digital Twins Performance juega aquí un papel clave, junto a MindSphere, el sistema operativo IoT abierto y colaborativo de Siemens, basado en la nube. MindSphere permite agregar, analizar y transformar los datos generados por el producto, la cadena de producción y el rendimiento, y planificar todo el proceso para conseguir una optimización completa.
"IoT MindSphere trabaja en tres ámbitos: MindConnect, que recibe los datos creados por las propias máquinas, los sensores y los equipos automáticos, y los almacena en la nube de manera segura para que puedan ser utilizados por sus propietarios; MindSphere, el sistema operativo abierto capaz de integrar aplicaciones de los clientes de manera también segura; y MindApplications, un espacio donde se ubican las aplicaciones creadas por nuestros clientes y que solo ellos podrán usar", comenta Mrosik.
Concentración
El mercado va conociendo cada vez más plataformas dispuestas a propiciar la digitalización de la industria, "pero habrá una concentración y finalmente van a sobrevivir muy pocas, quizás solo dos. MainSphere es una plataforma donde todos los desarrolladores pueden trabajar, y a nuestros clientes actuales y potenciales también les interesará porque invertirán en sus aplicaciones y las podrán situar en una espacio digital abierto. Tenemos una base muy sólida para pensar que nuestra plataforma será una de las que lideraran el mercado: conocemos cómo funcionan muchos productos porque los fabricamos, y Siemens es la mayor industria de software. Es la única empresa del planeta que trabaja en el mundo real y en el virtual a la vez", concluye el directivo de Siemens.
Arquitectura tecnológica
Siemens proporciona una veloz conectividad de la maquinaria de una factoría a través de los edge devices de MindSphere, que calculan con rapidez y extraen conclusiones en tiempo real desde las propias máquinas, sin necesidad de enviar previamente los datos a la nube. "Es la arquitectura tecnológica moderna", afirma Mrosik.