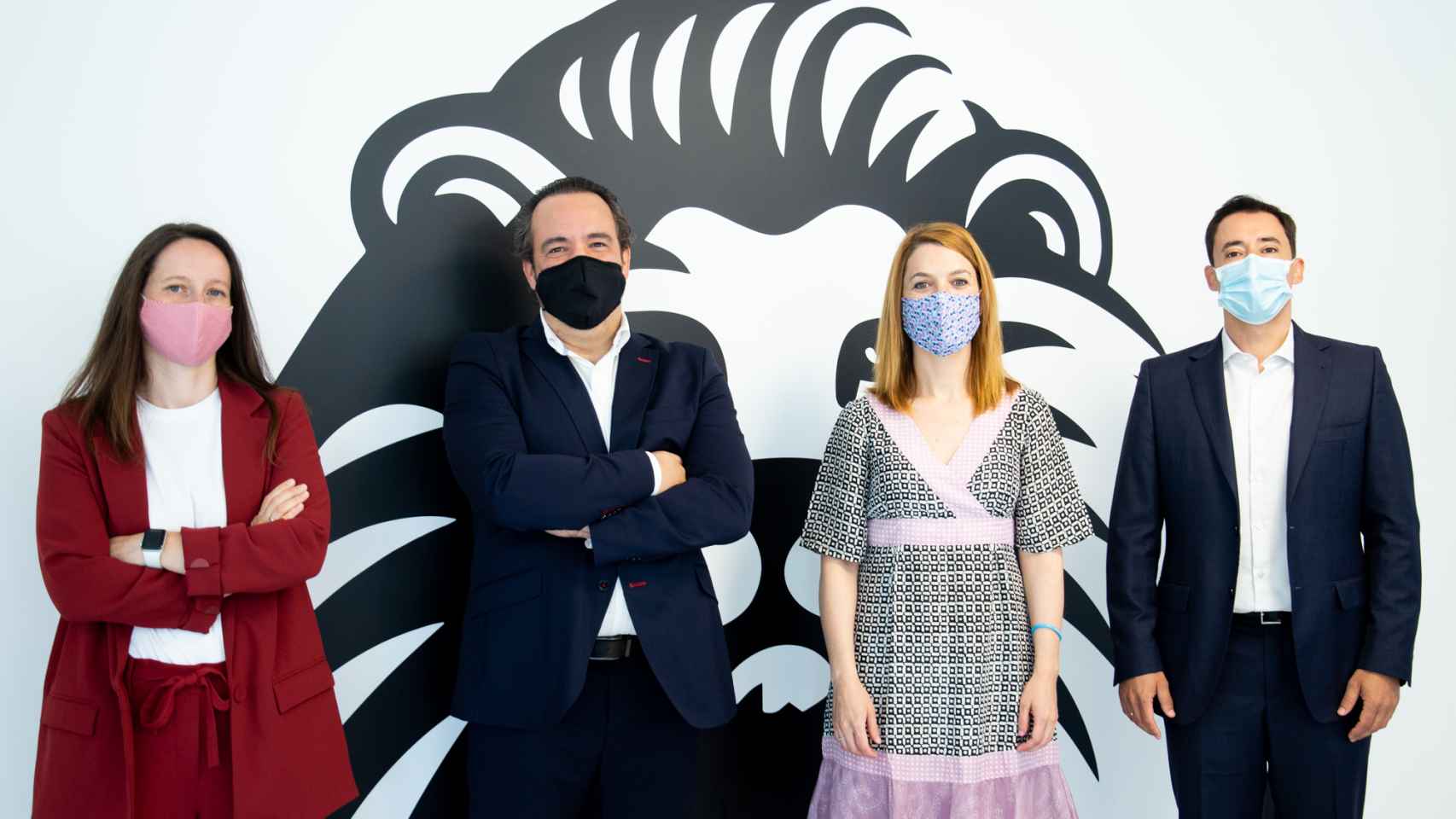
Los ponentes en la mesa redonda sobre industria 4.0 de D+I. De izquierda a derecha, Ana Benavent (directora de I+D+i de Valoriza Medioambiente/Sacyr), Alejandro Solana (director técnico de Nutanix Iberia), Susana Pérez (responsable de Factory Learning en Tecnalia) y Francisco Bernardino (director de industria en Ferrovial). Foto: ESTEBAN PALAZUELOS
Industria 4.0 para ‘simplificar, automatizar y optimizar las cadenas de producción con datos en tiempo real’
Expertos de Ferrovial, Tecnalia, Sacyr y Nutanix desentrañan todo lo que cambia con la llegada de la digitalización a las plantas modernas.
13 julio, 2021 02:13Las tecnologías facilitadoras de la innovación, a medida que cobran peso y se extienden, van configurando una nueva estructura industrial que hace dudar si es el momento de la Industria 4.0 o ya toca saltar a la versión 5.0.
Son cambios patentes que hacen visible que "hay una diferencia abismal entre las fábricas nuevas, de los últimos cinco años, y las de hace 50", según palabras de Francisco Bernardino, director de industria en Ferrovial.
Bernardino fue uno de los cuatro intervinientes en una mesa redonda organizada por D+I para hablar sobre la Industria 4.0. Los otros tres participantes son Susana Pérez, responsable de Factory Learning en Tecnalia; Ana Benavent, directora de I+D+i de Valoriza Medioambiente, perteneciente a Sacyr; y Alejandro Solana, director técnico de Nutanix Iberia.
Una conversación en la que lo primero que queda claro es que la tecnología "se ha convertido en una necesidad", dice Alejandro Solana. "Sobre todo en el contexto de la pandemia, en industrias con muchas ubicaciones remotas, para simplificar, automatizar y optimizar todas las cadenas de producción con nuevos tipos de información basada en el vídeo, realidad aumentada y otros, y poder tomar decisiones en tiempo real".
Simplificar la complejidad
Solana apunta, para comenzar la conversación, la necesidad de "romper fronteras" en entornos especializados en los que se crean silos.
Considera el directivo de Nutanix que la transformación digital es la oportunidad para "permitir la comunicación de tecnologías, procesos y personas, para sacar el máximo partido". Comenta que cámaras, instaladas en su día en fábricas como elemento de seguridad, son utilizadas ahora en algunos casos "para chequear el proceso, con identificación de las imágenes en movimiento y obtener con inteligencia artificial patrones de comportamiento e identificar fallos".
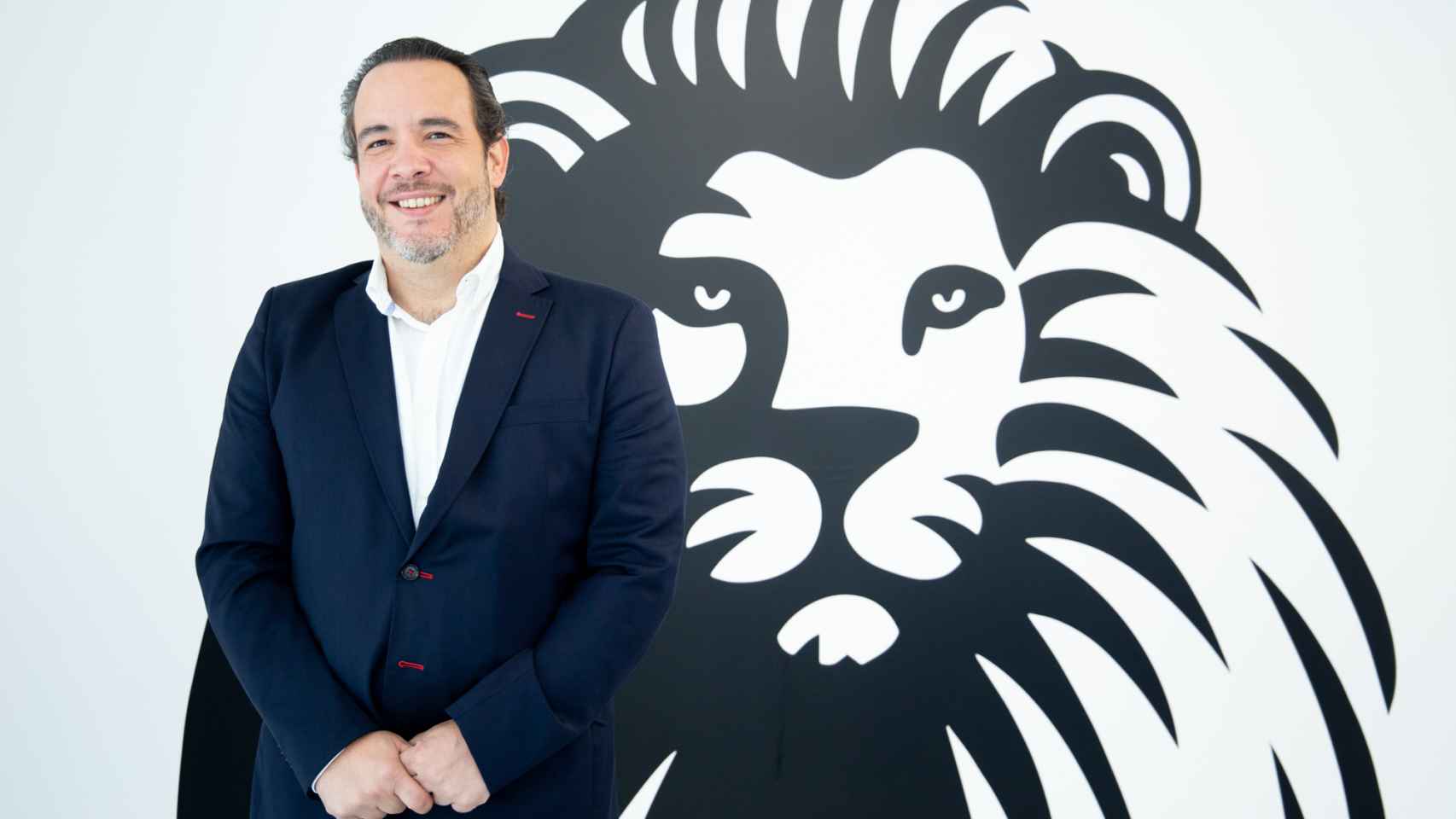
Alejandro Solana, director técnico de Nutanix Iberia.
Su receta es buscar "una aproximación horizontal. Simplificar, reducir silos y complejidad, para que fluya la información de forma natural y sacarle el máximo partido tomando decisiones en tiempo real".
Lo que propone son "plataformas simplificadas, donde todos los servicios están prácticamente de forma nativa en la propia plataforma. Todo aquello que es un 80%, tarea muy repetitiva, común en todos los silos, tenerlo de la forma más industrializada, automatizada y estandarizada posible. Y el 20% que es especialidad, en una arquitectura lo más estándar posible. Que el plano de control sea exactamente el mismo para cualquier ubicación y poder desplegar nuevos servicios de manera de manera muy ágil".
La representante de Tecnalia, sin discrepar, puntualiza dos cuestiones, "en cuanto a arquitectura" porque hay "enfoques híbridos. No vale lo mismo una arquitectura 'cloud' si produzco cada tres segundos una pieza, que necesito una respuesta anticipada y que el modelo de predicción conteste en tiempo real. En cuanto al 'edge', tiene sus capacidades de cómputo más limitadas".
Pérez espera que la implantación del 5G abra "una nueva puerta" para "aplicaciones demandantes de muy baja latencia".
Derribar silos
Queda claro que "hay entornos más maduros, que por su propio proceso productivo han necesitado invertir en tecnología", pero en el contexto actual "es una auténtica necesidad para la supervivencia".
"Es por sectores. La madurez no es homogénea", refuerza Susana Pérez. "Pero yo creo que nadie se va a quedar atrás, por el empuje sobre todo de tecnologías que unen los sistemas de planta, OT, con la parte IT, para homogenizar, integrar un montón de fuentes de información que estaban aisladas y derribar esos silos y pequeños sistemas de control dentro de las plantas productivas".
"Es un reto superado por algunos sectores y ahora da pie a que haya proyectos de mayor calado en explotar la información, aprovechar el control y mejorar procesos. Se está poniendo de manifiesto el impacto que tiene en beneficios", sentencia Pérez.
Francisco Bernardino se anima incluso a "sacar pecho" y afirmar que "la industria 4.0 española es top". Asegura que a nivel europeo y mundial es pionera "en implantar tecnologías e innovar". Pero echa de menos "inversión" y "empuje" para "digitalizar las fábricas más antiguas, de los años 70 y 80, y ponerlas al nivel de las nuevas". Declara su fe en el talento de las generaciones que llegan "empujando y son 100% digitales", y pone su esperanza en los inminentes fondos Next Generation.
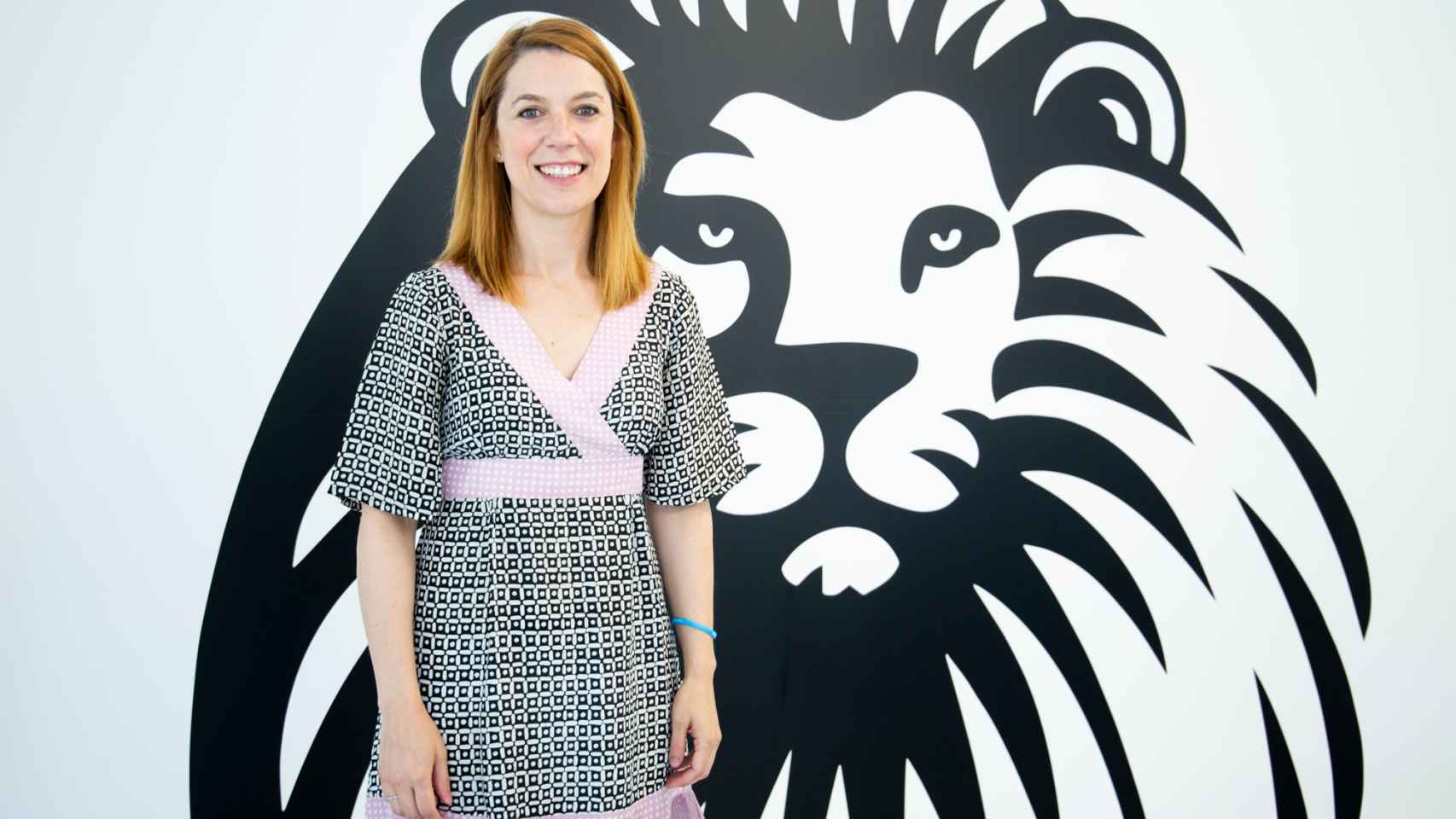
Susana Pérez, responsable de Factory Learning en Tecnalia.
A Ana Benavent le toca admitir que en su sector, el de los residuos y reciclajes, van "pasito a pasito, un poco a lo caracol", con poca inversión, por "el tipo de contratos que normalmente rigen ese tipo de instalaciones, con unos márgenes ajustados", que deja pocos recursos para sensorizar las plantas.
Sensores predictivos
Aun así, afirma Benavent que también están desarrollando "pilotos con sensores, procesando la información y obteniendo resultados en la predicción de roturas y para mantenimientos que ya no son preventivos, sino predictivos. Sabes cuándo se va a romper y te ahorras paradas de producción, que al final son pérdidas".
Otra cuestión que se plantea es que los sensores que hasta ahora había en algunas fábricas "para minimizar fallos, eran un poco de andar por casa", apunta Bernardino, que ahora sí ve un cambio de su aprovechamiento. Cree que los datos se recogen ahora "mirando al futuro, al big data y al análisis".
Pérez añade desde su actividad, consistente sobre todo en "hacer transferencia [de conocimiento] al ecosistema industrial", que ahora se está produciendo "una explosión" de la que se ve el impacto y se mide. Se ve el gran beneficio de implantar" la digitalización. Aunque lo prioritario es "definir un objetivo", no "digitalizar por digitalizar". Advierte Pérez que "hay muchos retos", incluido el de la integración de los trabajadores.
'Humankind in the loop'
La otra cuestión "son los temas de sostenibilidad, circularidad y reaprovechamiento", en lo que se está desarrollando una de las líneas de aplicación de la IA para reducir desechos, segundos ciclos de producción e incluso aspectos de consumo energético.
En este punto, Susana Pérez introduce en el debate el factor humano, "el concepto de humankind in the loop", el hombre como parte del circuito de producción. Modelos de aplicación que aprenden del feedback humano: "El propio operario es preguntado, e interactúa con la aplicación que está desplegando. El operador tiene el conocimiento de la experiencia de años que lleva ahí, que no se suele trasladar al entorno virtual".
Ese problema, "ahora se intenta revertir. También hay ciclos de despliegue ágil con self learning. Cualquier dato nuevo que pasa por el modelo lo reentrena para aplicarlo y corregirlo", añade. La disponibilidad de nuevas opciones para captar datos, sonido, vídeo, temperaturas, amplia el abanico de recursos para controlar el funcionamiento de los sistemas.
Desde la experiencia de Ferrovial como empresa de servicios, Bernardino observa que el momento está superando la vieja rémora de que un operario, eficaz y experto con una máquina, no fuera capaz de trabajar en otra fábrica.
"Ahora el usuario es versátil", afirma. "Es un usuario conectado que puede trabajar de forma remota. La tecnología ha ganado en ser mucho más amigable, mucho más usable. Nosotros estamos trabajando en una forma remota, que hace 15 años era impensable. Tenías que tener localizado con el móvil la furgoneta, la herramienta… incluso, muchas veces, los primeros softwares de control de diagnóstico eran exclusivos de una marca o de un equipo concreto. Necesitabas hasta tres ordenadores distintos".
Añade que otro reto es "transformar al personal", con la ventaja de que "la gente que se incorpora al mercado laboral es digital, capaz de absorber cualquier conocimiento". Pero, a cambio, "hay una generación que todavía le falta para llegar a una edad de jubilación, a la que hay que, no tanto digitalizar, sino enseñar a trabajar con tecnologías más sencillas".
Robotización
Benavent subraya que el sector residuos está "poco robotizado", pero está lleno de tareas muy penosas que puede hacer la máquina. "Introducir un robot es para ellos [los empleados que ahora lo hacen a mano]: ¡jolín es que me está quitando el puesto de trabajo!", exclama.
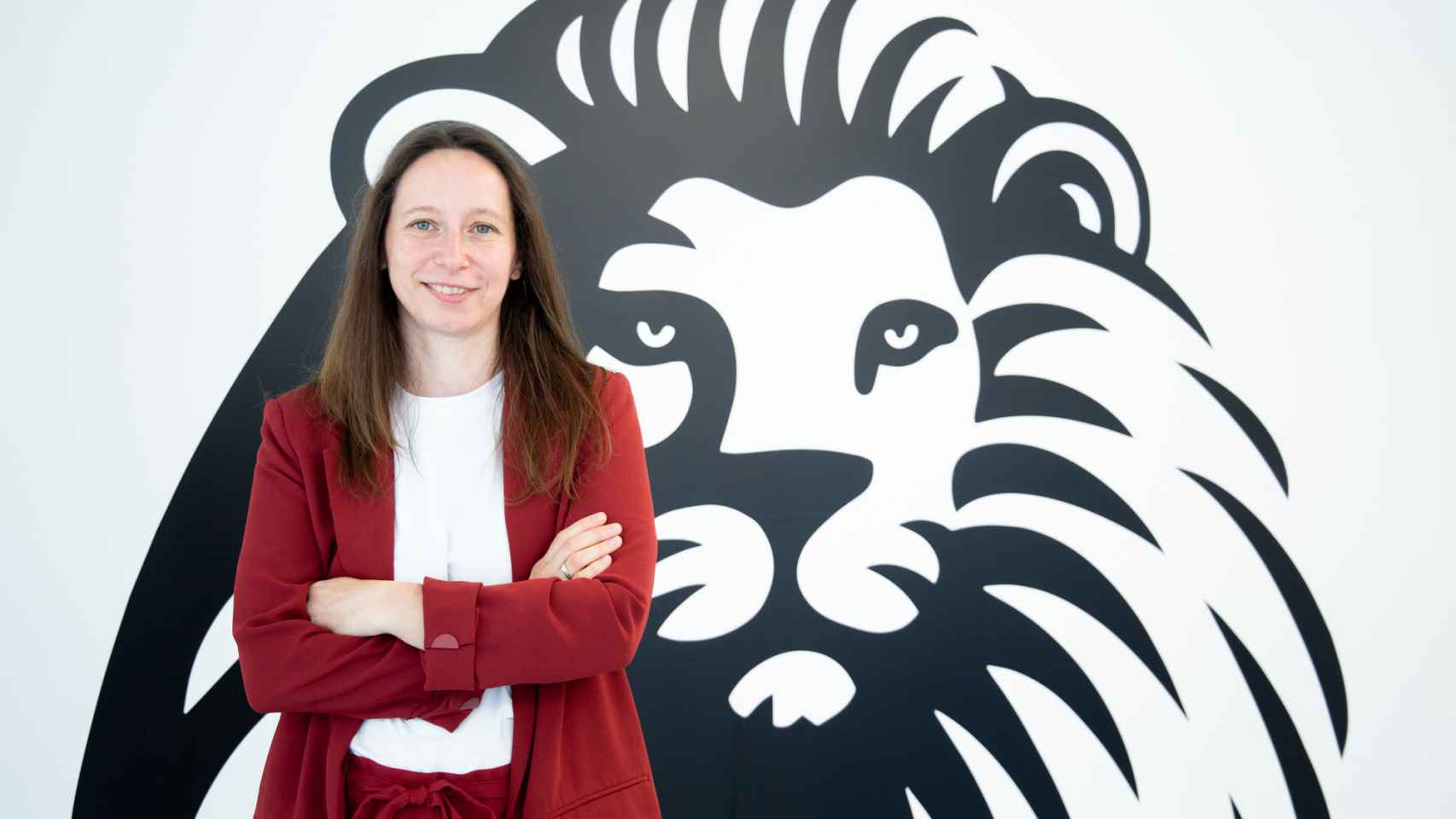
Ana Benavent, directora de I+D+i de Valoriza Medioambiente (Sacyr).
Plantea la necesidad de convencer al trabajador de que puede dedicarse a otras cosas, para facilitar el funcionamiento de la instalación, y que acepten "que esto viene para quedarse y para mejorar su calidad de trabajo. Es una oportunidad para reciclarlos en otras cosas y beneficia a la industria".
De paso, Benavent explica que "cada planta es un mundo que estandarizar. Cada cliente tiene unas necesidades, cada proceso es diferente, e incluso cada tecnología dentro del mismo proceso, en cada fabricante es totalmente diferente. Bueno, es lo mismo, pero sus equipos funcionan diferente".
Para homogeneizar los datos, en Valoriza Medioambiente han tenido que "invertir mucho tiempo en crear una 'piedra roseta' para que la información se traduzca y se pueda introducir en un sistema para poder llegar a una operación en remoto que en el sector no ha ocurrido todavía".
Los casos de éxito presentes
Dando un repaso a algunos casos de éxito, la representante de Sacyr menciona "un piloto en una planta de [procesamiento de] neumáticos" desechados, donde han instalado sensores para medir temperatura y vibraciones. Con ellos puedan predecir roturas de la tritura.
"Esos sensores son fabricados en España por una empresa española. Se autogeneran la electricidad por diferencia de calor entre la superficie de contacto del equipo y el ambiente y transmiten los datos wireless, con lo cual te ahorras dos cableados", detalla.
"Teníamos toma de temperatura, pero no de vibración. Y estamos viendo que, lo que antes hacía un operario por cómo sonaba la trituradora, ese sensor lo hace con éxito. Es una tecnología que vamos a adoptar en toda esa línea de producción", remacha.
Otro caso, en la misma planta, es la "identificación por imagen" en "ese mismo molino" al que "se le rompen los dientes porque tritura neumáticos que tienen dentro hierro", relata Benavent.
"Una cuchilla rota te rompe la matriz del pulverizador". Lo cual supone también "rotura de la producción, pérdidas económicas…". Las cámaras que identifican imagen con inteligencia artificial "también funcionan". Si bien, Benavent advierte que todavía lo están perfeccionando. "En nuestro caso, es un éxito hacer ver que eso funciona, porque es un cambio cultural".
Inteligencia artificial para velar por los operarios
Ferrovial se anota como caso de éxito el desarrollo de la aplicación Expert Safety, "con inteligencia artificial, bastante sencilla, pero con una alta aplicabilidad", explica Bernardino.
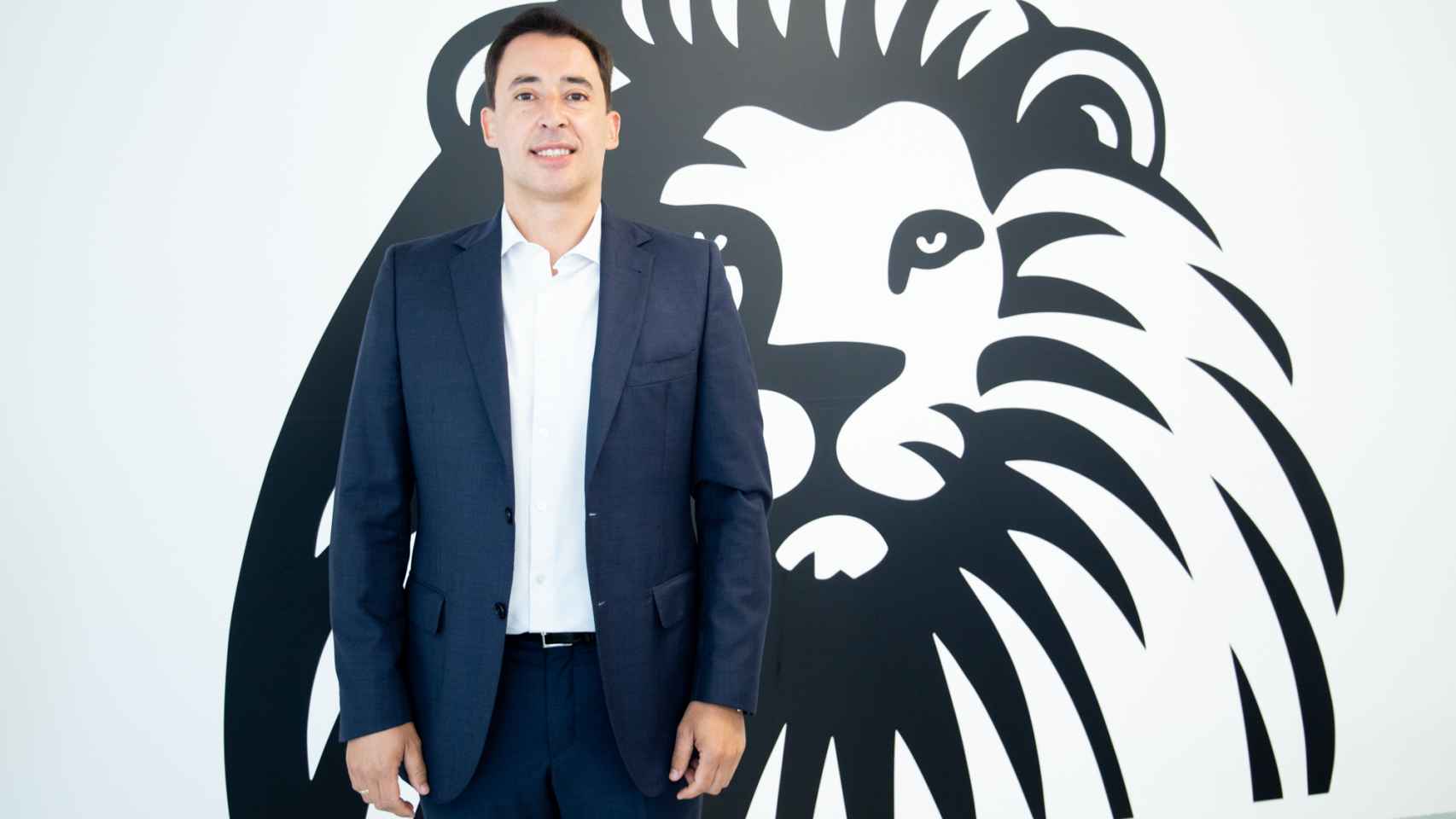
Francisco Bernardino, director de industria en Ferrovial.
La utilizan con las cámaras de las plantas donde trabajan, "con un algoritmo de machine learning que identifica cuando el trabajador lleva los EPIS y va debidamente equipado con gafas, mascarilla, casco, chaleco… O incluso cuando entra en zonas de cohabitación con carretillas o fuera de la zona de paso peatonal". La IA reporta cualquier incidencia en tiempo real.
Lo están "escalando" como "una aplicación de la tecnología que no sólo no viene a sustituir al hombre, sino que es para hacerle más fácil su tarea y más segura".
También relata un proceso de automatización de logística para Michelín, en el que la carga de neumáticos, "que pesan siete u ocho kilos", se hacía a mano, en un empleo en el que "sólo se permiten dos horas seguidas de trabajo" por el gran esfuerzo que exige.
Han desarrollado un autómata que hace la carga, lo que, admite Bernardino, "se puede ver como una sustitución del trabajador. Pero los robots vienen a mejorar las condiciones de trabajo y el reto está en transformar a ese cargador de neumáticos en operador del robot".
Repuestos con impresión 3D
También apunta a la tecnología de impresión 3D como una herramienta para "romper los silos de los fabricantes de repuestos" y mejorar tiempos de respuesta. "Muchas veces los repuestos vienen de Asia y el tiempo mínimo es de una semana a diez días. Nosotros tenemos un centro de impresión 3D. Somos capaces de escanear la pieza y fabricarla en 20 o 24 horas. Es un salto abismal en mejora de la productividad".
También Tecnalia ofrece un caso de mantenimiento predictivo en remoto, para palas de aerogeneradores, mediante ultrasonidos que monitorizan los rodamientos y anticipan el riesgo de rotura. Esto añade la ventaja de ahorrar visitas de inspección y que el técnico, cuando tiene que ir a reparar algo lleva de antemano la información del estado de la maquinaria.
Otro caso que cita Pérez es un sistema de seguridad para entornos en los que hay riesgo de explosión. Los trabajadores llevan un wearable que los mantiene localizados y, mediante un sistema de balizas, se puede saber cuántos están en la zona, los que entran y los que salen.
Además, Pérez comenta experiencias del mundo de la automoción, con sistemas de simulación desarrollados hace años para establecer los procesos de fabricación de piezas. Gracias al nuevo flujo de recogida de datos, se puede hibridar un sistema en el que el software de simulación aprovecha y aprende del feedback que recibe en tiempo real de cómo funciona el proceso.
Y aún añade otro caso real, en la industria alimentaria. Se trata de una fábrica de pasta, con turnos 24/7, en la que se tomaban muestras aleatorias, para hacer pruebas de calidad. Se enviaban al laboratorio y tardaban cuatro horas en estar disponibles los resultados. En caso de una deficiencia era preciso tirar la producción de las últimas cuatro horas.
Para mejorarlo, analizaron las variables químicas que actúan sobre el producto, las monitorizan y han entrenado un sistema de IA, capaz de predecir el estado de la muestra en tiempo real.
"Siguen haciendo la media de laboratorio, por asegurarse, pero lo mantienen dentro del umbral [de calidad correcta] y se aseguran que no tienen que tirar una producción terminada", concluye Pérez.
Los próximos 25 años
Ahora, con los fondos europeos a la vista, Francisco Bernardino se anima a considerar que se va a concretar "un cambio radical que va a marcar los próximos 25 años para la industria, no solo en procesos productivos, sino en tecnologías".
Susana Pérez cita un informe de Forbes, que dice que el 80% de la fuerza de trabajo de una empresa productiva son empleados que no están en un escritorio, con un ordenador o un móvil. Y, sin embargo, la inversión en herramientas software para ese perfil, que "necesita tener las manos libres" es del 1%. Lo cual sugiere la necesidad de desarrollar "sistemas con una interacción más inmersiva" para dar soporte a ese perfil.